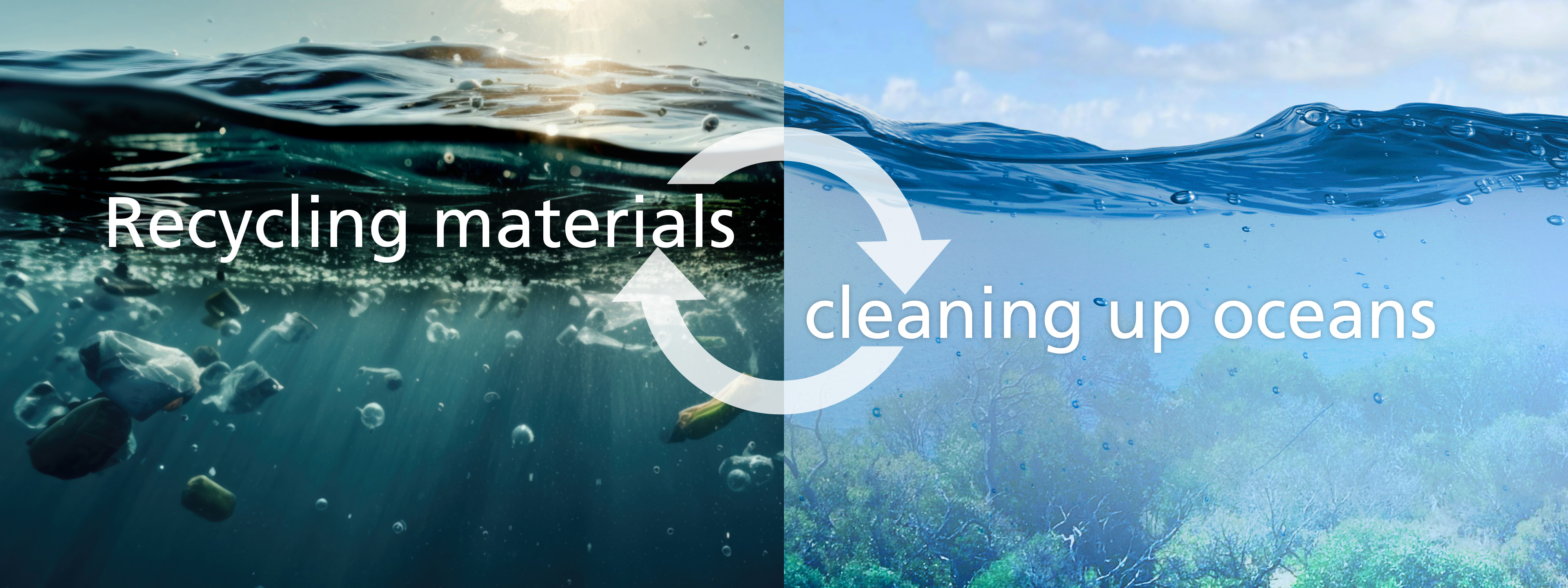
Most marine litter in the world is made of plastics
Unfortunately, a large part of marine food is made of plastic. Plastic breaks down into several parts and can be divided into nanoplastics and microplastics. Nanoplastic is the smallest part that sinks deep into the ocean and lands on the plankton. Microplastic is the larger part, which spreads over the water like a soup and is consequently also eaten by marine animals.
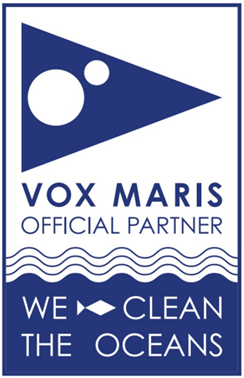
The VOX MARIS project, developed by the BioDesign Foundation, is the latest technology to recycle global tonnes of plastic that end up in the ocean. The BioDesign Foundation is a non-profit organisation and always proclaims a message of hope and positivity. BÄR is pleased to be able to support the project financially and to work with VOX MARIS as a cooperation partner. In this way, BÄR is making a significant contribution to the revitalisation of the oceans.
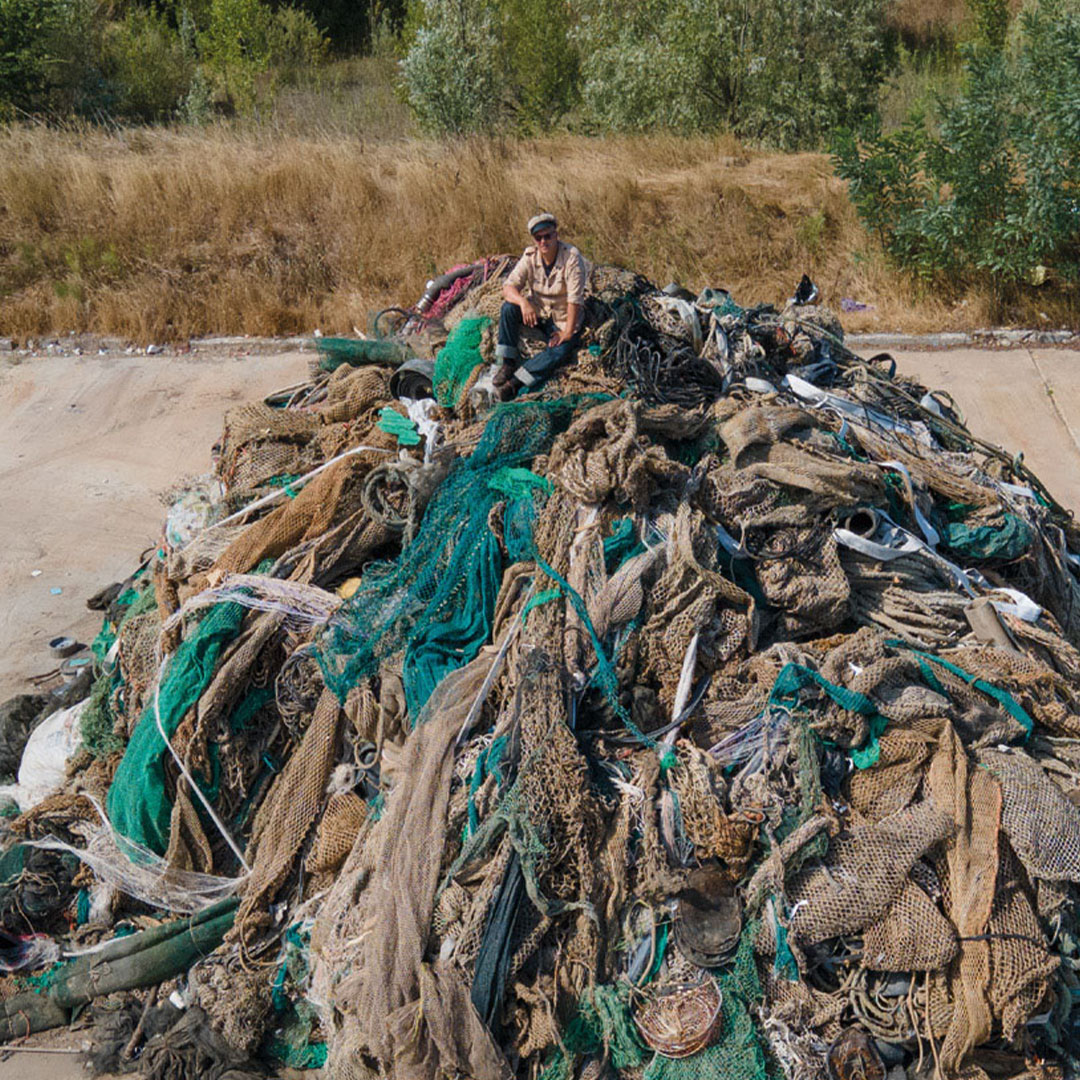
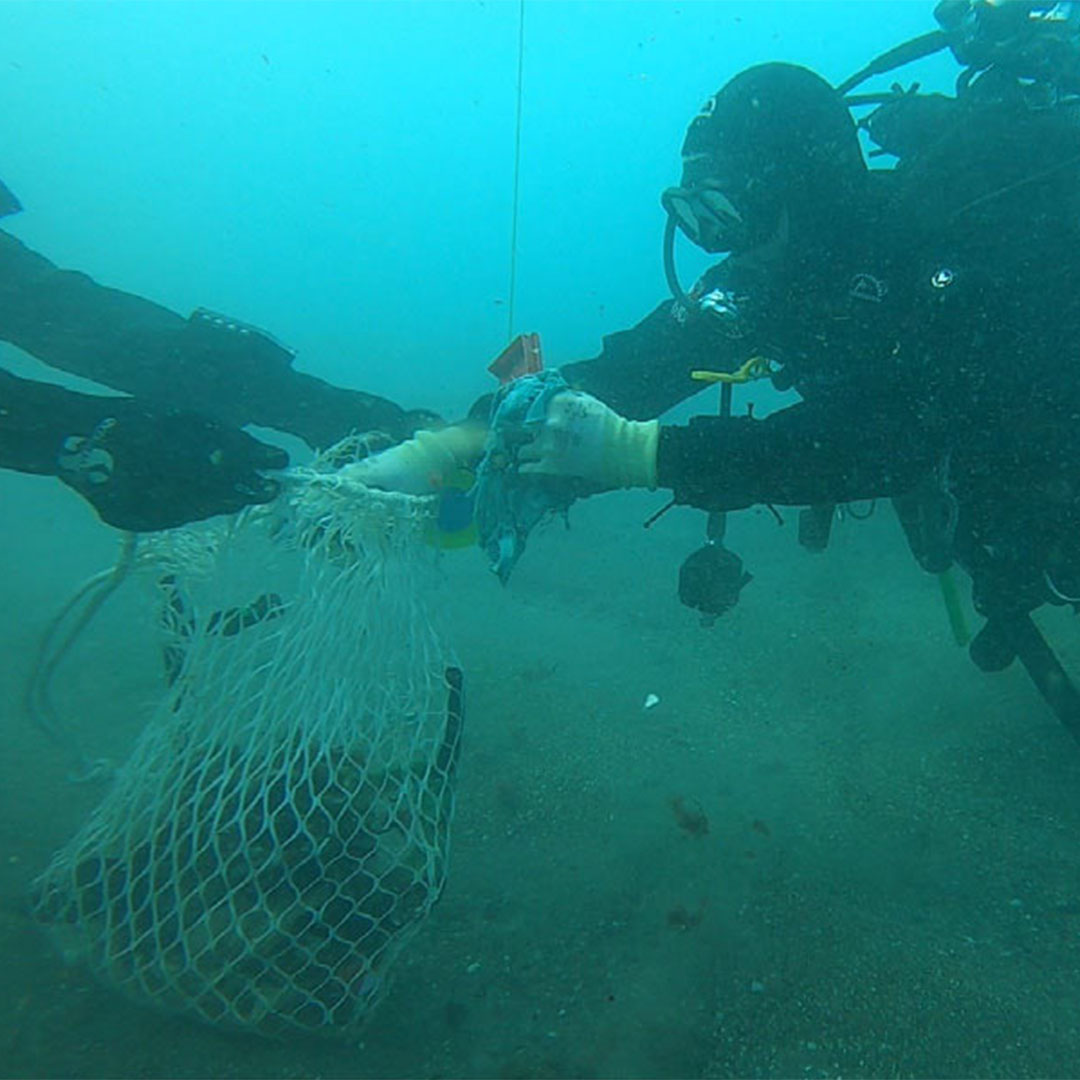
Recovering the lost plastic
100 kg of plastic is caught by fishing boats every day. To encourage recovery, fishermen are paid for the plastic they catch. The boats bring their plastic catch back to the HARBOUR COLLECTION CENTERS at the harbour. In Italy, a partner has been found to make the dream of cleaning up the oceans a reality. With a research team that has been working for more than 10 years on the development of a prototype for a thermocompacting system, it is possible to start this recovery of the lost plastic.
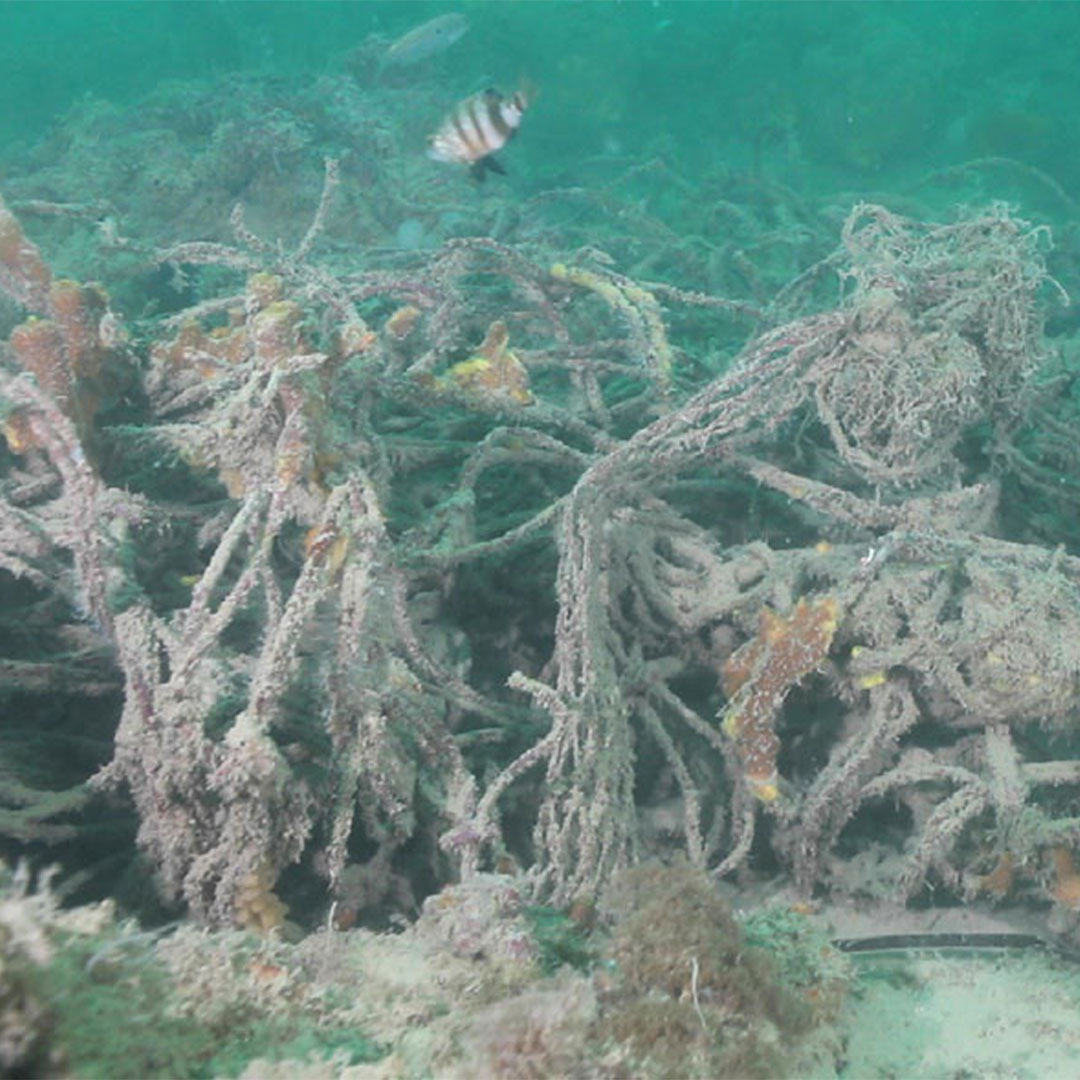
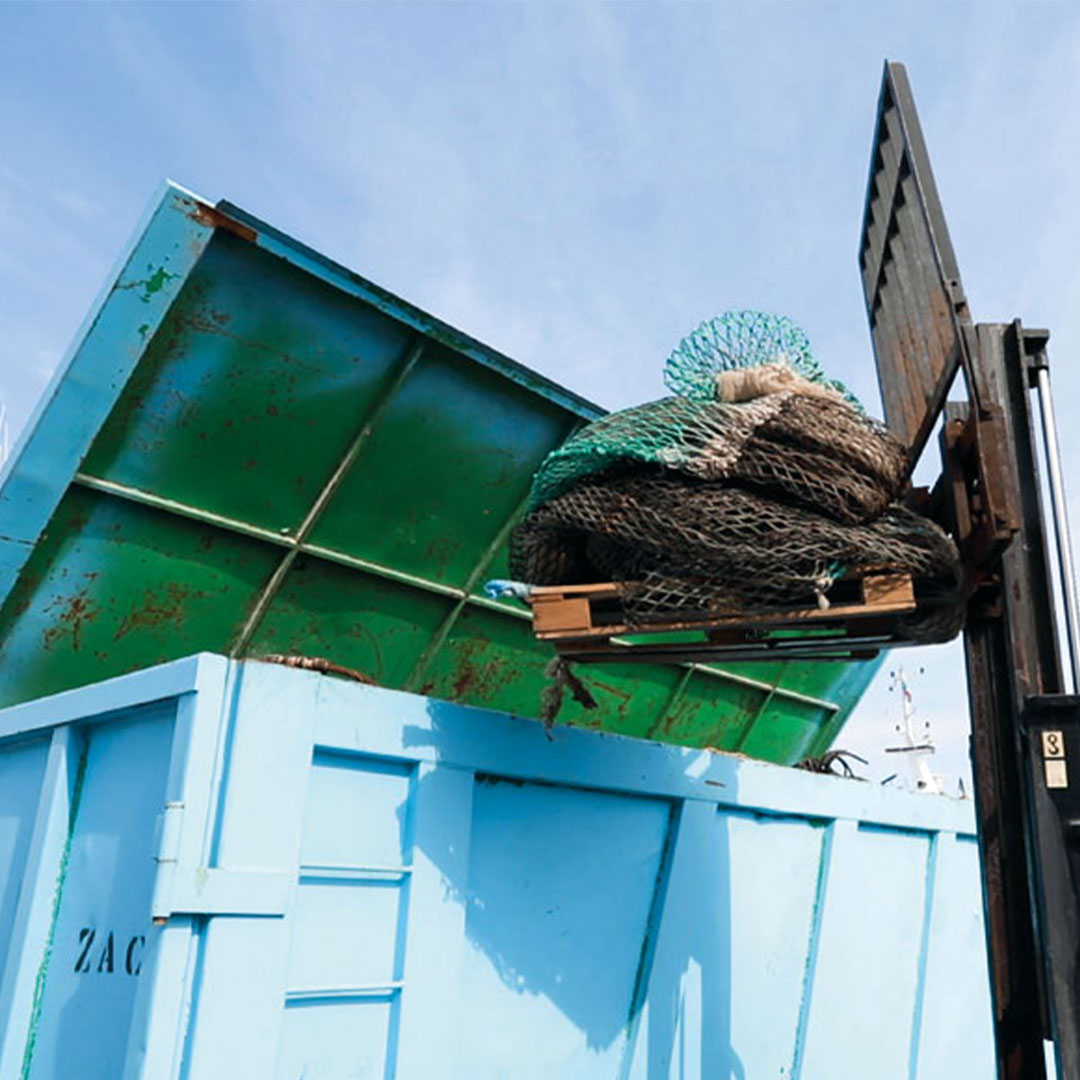